Researchers develop new technology to reduce carbon emissions from steelmaking by nearly 90%
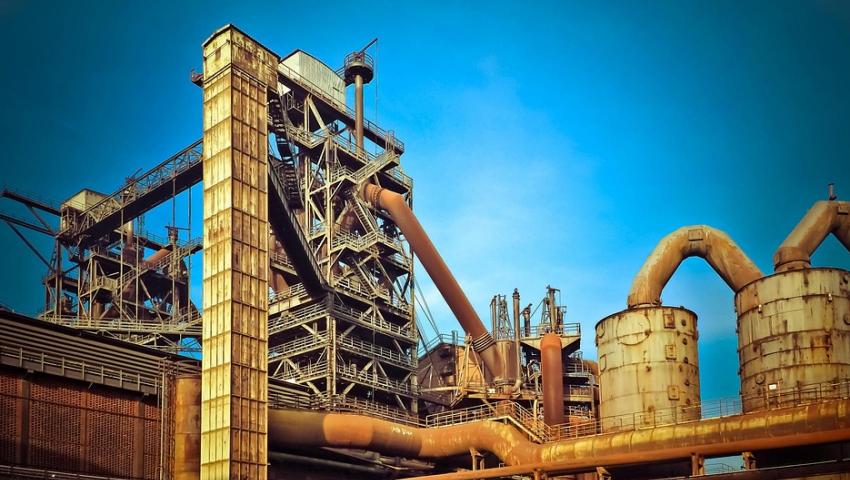
Source: Pixabay
Researchers from the University of Birmingham propose a new modification of traditional iron and steel furnaces that can help reduce carbon emissions from steelmaking by nearly 90%, reported industryinfo.bg.
The drastic reduction in emissions is achieved through a "closed" recycling system that can replace 90% of the coke normally used in blast furnaces and produce oxygen as a by-product.
According to the researchers, implementing the modification in the UK alone could contribute to reducing costs by £1.28 billion over 5 years and the country's total emissions by 2.9%.
"Current proposals to decarbonise the steel sector rely on phasing out existing furnaces and replacing them with electric arc furnaces powered by renewable energy. However, the cost of building an electric arc furnace can exceed £1bn, making replacement economically unviable with view of the timelines for achieving the Paris Climate Agreement targets. The system we offer can be adapted to existing furnaces, reducing the risk of asset lock-in, and the reduction in both carbon emissions and costs is felt immediately.", commented Prof. Yulong Ding.
Iron and steel mining are among the largest sources of carbon dioxide in the foundry industry, generating 9% of global emissions. According to the International Renewable Energy Agency (IREA), the sector needs to achieve a 90% reduction in emissions by 2050 to limit global warming to 1.5°C.
The University of Birmingham has applied for a patent for the system in the metal mining sector and is looking for long-term partners for the implementation of pilot projects, application of the technology in existing facilities or for its further development, reports the University of Birmingham.