Gabriel Stanciu, Alstom: We start with the long-term ‘health’ for the trains in Bulgaria in Q1 2021
The innovative technologies contributes to safer and more efficient traffic – allowing an increase in traffic capacity by over 25%.
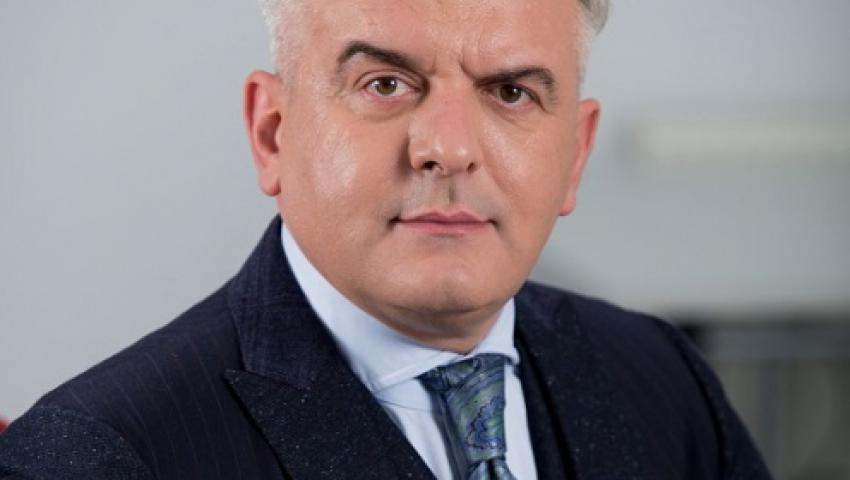
I think the mid-level of professionals in the institutions running these projects are in great need of specialised training, and also they need to take responsibility and push for these processes to happen, tell us in interview Gabriel Stanciu.
Gabriel Stanciu is Alstom Managing Director for Romania, Bulgaria and the Republic of Moldova. He is also the president of the Railway Industry Association in Romania (AIF). With a cumulative experience of 25 years in industrial management, his journey at Alstom began in 2005, when he was appointed general manager of Alstom Transport Romania. Gabriel Stanciu holds an Executive MBA diploma from ASEBUSS, and his university studies cover multiple fields (electronics and telecommunications, international economic relations and law). In his opinion, a successful manager is the one who leads by example and who encourages initiative and personal responsibility among his team.
In Romania, Alstom has been active since 1994 and it currently employs over 500 people. The company is responsible for the modernization and maintenance of the Bucharest metro rolling stock, as well as for complex infrastructure and signalling projects, as part of the modernization of the national railway network.
Mr. Stanciu, recently you reported on the progress of the five-year contract with BDZ- Bulgaria, concluded last year for the modernization of 46 electric and diesel trains in Bulgaria. What were the activities you managed to complete and what were the challenges?
The maintenance program for the national passenger fleet is Alstom’s first project on the Bulgarian market and for us it is extremely important the trust we build, both with our customers from BDZ Passenger Services and with our partners and suppliers.
We are pleased to announce that despite the unexpected difficulties and delays caused by the global pandemic crisis, the project has advanced significantly in the recent months. Between December 2019 when the contract was signed until September 2020, we have made great efforts to modernise and equip three depots - in Sofia, Varna, and Plovdiv. This is a very important preliminary stage before the beginning of quality maintenance activity, and it was the result of a large investment made to ensure suitable conditions. After that, we started regular maintenance services for 26 out of the 46 trains and began works on some immobilised trains so that they can be included in daily train schedule after many years of absence. The maintenance activity is a 24/7 process that requires serious expertise and considerable efforts. The present results were achieved thanks to a solid team work of Alstom employees and local suppliers together with the customer and the Group’s maintenance experts.
What are the most important activities for the next few months? What goals have you set and in what terms do you expect to achieve them?
Our ultimate goal is to provide professional maintenance for the BDZ passenger fleet and extend its life by up to ten years. Maintenance is a continuous activity, and the overall result is an increased availability of the fleet. A professionally conducted maintenance programme is a guarantee that the rolling stock is used efficiently, and the downtime is reduced as much as possible.
The maintenance team are making serious efforts to repair 4 diesel trains that have been immobilized for a long time, to re-launch them in circulation as soon as possible. The contract includes a total of six such trains, and we already have 4 of them well advanced. We are also doing preparations and ensure necessary equipment and materials for the overhaul of the entire fleet, scheduled to start in Q1 2021, in accordance with a clearly set maintenance timetable. This is a very important part of any maintenance project because it ensures long-term ‘health’ for the trains. We also continue to build a solid network of local suppliers, which are important in a successful maintenance project.
How many full time jobs are you planning to create, at what kind of positions? When? Did you open the office in Sofia-Bulgaria?
This project with BDZ Passenger Services definitely creates jobs on the Bulgarian market, more than 50 people being now involved 100% in this project. We opened the office in Sofia earlier this year and we have hired people, in spite of the difficulties generated by this pandemic. We now have a very good and dedicated team of Bulgarian employees – and many are in technical jobs, for example we have a dedicated Bulgarian project manager – and we have also local suppliers who support the project. In the overhaul phase, that is planned to start first quarter of next year, the required workforce will increase.
Why is the railway sector in Bulgaria still not at the required European level?
Like all the countries in the region, Bulgaria is making progress, but the needs are still too great in railway infrastructure and rolling stock and it looks like things are changing too slowly. In fact, change is happening, but we would love to see everything changing overnight, and that’s not possible. It takes a lot of investments to upgrade everything and it also takes a lot of expertise to prepare good documentation, to organise tenders and see them through. I think the mid-level of professionals in the institutions running these projects are in great need of specialised training, and also they need to take responsibility and push for these processes to happen. Instead of postponing things, it’s better to speed them up. A good infrastructure always positively impacts the economy, the development of a country.
What is the experience of the company in other countries, indicate the progress in the Romanian sector. What is the development of the railway infrastructure and the modernization of the railway transport in Moldova?
Romania is making progress in railway rehabilitation – we have a European corridor, Rhine-Danube, in full rehabilitation on its Northern branch and the Southern one will follow, to increase the speed of passenger trains to 160 km/h and for freight trains to 120 km/h. We equip the lines with the latest European signalling system, ERTMS level 2. We also need new trains for passenger rail transport in Romania, there are some tenders ongoing but they are not finalised yet. Latest news is that we have just signed the first Alstom contract for rolling stock in Romania – for metro trains on a newly built line in Bucharest. So things are happening, but again, maybe not as fast as we’d like, as citizens of a certain country. The opportunities are great and we need to see the positive side of this. Regarding Moldova, the opportunities are also great but so are the challenges, mainly because the investments needed for such infrastructure upgrades are lacking and also because the standards are significantly different. We are currently looking to close a significant deal in Moldova, but we will get back to that when it shall be concluded.
When and throughout the country will passengers be able to see the visible effect of modernization? What additional functions of the trains will be installed? What new amenities will there be for drivers?
The contract with BDZ is primarily for full maintenance services – which essentially means securing the required availability of the fleet in accordance with the traffic schedule, to make sure that the trains are able to run safely and in top condition. Another component – quite important – is the reintroduction into circulation of six diesel trains that have been long immobilised and now will be able to re-enter operation, with changed motors. Thirdly, a genuine modernisation will be seen in the electric multiple units, where we will install new technology, new functions such as wifi for passengers, as well as modern interior/exterior lighting system using LED technology. This upgrade will be extended to the whole fleet and later on it will be updated with more additional features, such as new passengers’ information systems and new driver desk displays.
What are the innovations in the technologies that you will offer in Bulgaria as well, are there any new systems for management and notification of the railway system?
If you are referring to digital traffic control solutions, we haven’t had the chance to introduce our technologies yet to the Bulgarian railway, as the tenders so far focused mostly on the civil works upgrades required by the infrastructure. As Alstom is a leading player in technology for sustainable mobility, we would love to have the opportunity to contribute to Bulgaria’s modernisation from this point of view. For example, in Romania we delivered the country’s very first modern digital control centre, and two more are on the way, in two other projects that we implement. This contributes to safer and more efficient traffic – allowing an increase in traffic capacity by over 25%.
What environmental characteristics will the new railcars meet, will they pollute the environment less, what filter technologies are used to reduce carbon dioxide in the atmosphere? Would you compare it to pollution before modernization?
If you refer to the maintenance contract, we can’t really talk about new trains, as much as we’d like, but well-maintained trains of a certain age, that will still be able to operate safely for many years to come. A diesel train that is kept in a good condition and which is able to observe the standards for which it was built is a reliable train and it doesn’t affect the environment more than it should. If you talk in general about the new trains vs older generations, the technological leap has been enormous. We are now talking about completely non-polluting rolling stock – such as the hydrogen-powered trains or the battery trains, both of which Alstom produces. In fact we are capable to offer the entire range of environmentally-friendly solutions. Moreover, many of our trains are recyclable to a great degree, over 95% – and this is also important for the environment.
What would be the applicable practice in our country for public-private partnerships in the field of railway transport for more successful modernization? To what extent is it the result of a management decision or an investment?
In a report from 2018 of the European Court of Auditors analysing the Private-Public partnerships in the EU, the conclusion is quite clear: in the absence of a very consolidated experience and expertise in implementing successful PPP projects – which only a few member states have -, there is a high risk that PPPs will not be as efficient as expected and “will not provide adequate value for money”, compared to a traditional acquisition process. So in the end the most effective manner of implementing transport-related projects remains the tendering.
One thing I would like to emphasize is that generally a low acquisition price doesn’t necessarily mean the best option, because in modern transportation what really matters is the cost of operation throughout the entire lifecycle. A good quality product or solution, although possibly more expensive at acquisition, with the proper maintenance measures in place, will serve the operator longer and more effectively than a cheap product that will have a lot of downtime and will require more effort and resources to keep in operation.
Why did Alstom choose Bulgaria? In which countries are your next expansion plans targeted? What new modernization programs do you envisage in the markets in which you operate?
Our involvement depends on the specific needs and priorities of railways operators in various countries. We work in the same way everywhere, we respond to specific requests when we believe that we can provide competitive solutions, we participate in tenders based on Alstom’s full expertise and broad range of solutions. So it very much depends on what a specific country is set to accomplish. We have operations in 60 countries across the world and we have high competences in all four key areas of expertise required in the transportation industry – from a complete portfolio of rolling stock, both for urban and mainline transport, to a full range of systems and infrastructure solutions, from signalling solutions which is now moving more and more into the realms of Digital Mobility – to of course an impressive portfolio of maintenance solutions. So we can respond to any needs of any transport operator, as long as they are expressed in a well-developed tender which we usually do our best to respond in the most competitive manner.