Зарядна станция под земята ще задейства скоро в рудник Челопеч
Първите електрически тежкотоварни машини са на път към България и стават част от подземните иновации в рудника
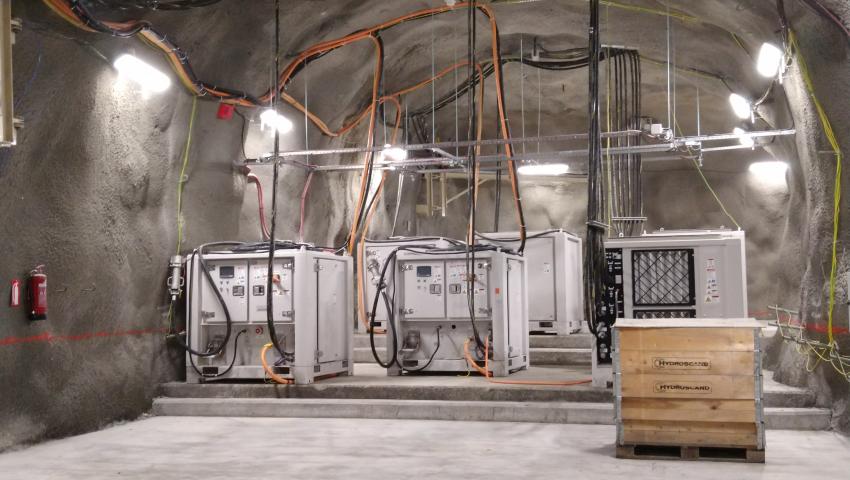
Снимки: Ива Иванова / 3eNews
Зарядна станция за тежки машини с електрическо задвижване, които да заменят дизеловите, е изградена под земята в рудник "Челопеч" и скоро ще влезе в експлоатация. Станцията е на 420 м. дълбочина под земята и е напълно оборудвана, видяха журналисти в Деня на отворени врати на "Дънди Прешъс Металс Челопеч". Има охладители, противопожарни системи и съответната прилежаща инфраструктура.
Първата машина, която ще се зарежда там - челен товарач, в момента пътува към България и скоро ще пристигне, а през декември рудникът ще се сдобие и с подземен електрически камион -дъмпер. Двете машини са с батерии, вместо с дизелови двигатели, така че ще генерират по-ниски емисии СО2, изтъкна директорът „Производство“ Николай Симонски.
Той уточни, че батериите са литиево-йонни, но техният принцип е по различен, така че да са безопасни за подземни условия. Това е нова технология и единици са рудниците в света, които ползват електрически машини. „Ние ще сме първите, поне в България, които ще ползват тази технология“, изтъкна той.
Същите машини в дизелов вариант – подземни челни товарачи и камиони- дъмпери са част от сегашния автопарк на рудника.
Товарачът е 30-тонен и кофата му загребва 10 – 12 тона руда, в зависимост от плътността й. С три кофи и половина пълни камион. Самият камион празен тежи 45 – 50 тона и като се натовари става близо 90 -100 тона. В рудника действат 7 такива челни товарача и 7 камиона. С електрическите, като пристигнат, ще станат 8 на 8.
Тези машини са оборудвани със системата AutoMine, която позволява теле-управление. „Операторът е извън машината и с дистанционно, като на детска играчка, може да управлява машината или като компютърна игра. Обучаваме машината да запомни своя маршрут под земята, слагаме виртуални бариери, които не позволяват тя или човек да премине и така се управлява от разстояние, в случая – 500 метра над нас операторът може да си седи в удобния стол и да си кара машината“, разказа Николай Симонски. Има и друга опция, продължи той - машината се обучава да познава своя маршрут и работи сама – отива, където трябва, загребва, връща се, сипва, а операторът само следи основните параметри.
Под земята машините са на мото-часове, не е като на Земята - на километри. На определени мото-часове има неща, които трябва да се проверят, ремонтират или настроят и всичко се комуникира чрез таблети, разказа главеният инженер „Мобилно оборудване и поддръжка“ Тихомир Бакърджиев.
„В реално време се следят всички параметри на машината и при евентуално излизане извън тях, получаваме нотификации в нашата система. Всичко става през таблета и в реално време, независимо, къде си. Вече 3 години не използваме хартия. Никой не иска хартията вече. Не е нужно да съм в Челопеч – просто ми трябва телефон със съответното приложение, за да мога да проследя как върви съответното обслужване“, разказа той.
В основното подземно депо случихме на дъмпер в техническа профилактика. „В момента този камион е на обслужване – миене на радиатори, проверка на системи, компоненти, подмяна“, поясни Бакърджиев.
„Такива машини няма на друго място в България и на много малко места в Европа ги има. Тук ние се учим всеки ден на тези машини. Нямаме поддръжка от типа - да дойде външна фирма, защото няма такава“, добави той.
По време на визитата си в рудника видяхме в работен режим и друга рядко срещана тежка машина - пробивна карета.
Още подземни иновации
"Дънди Прешъс Металс Челопеч" е единственият подземен рудник в света със 100% надеждно wi-fi покритие на 600 м. под земята. Дигиталните технологии са присъщи във всички дейности на рудника. За повече безопасност и точност, които са особено нужни под земята, компанията използва специален автономен дрон, разработен от нея в колаборация с Exyn Technologies и го демонстрира пред журналистите.
Този дрон сканира минните изработки и помага много на маркшайдерите да извършват ежедневните си дейности. Голяма част от изработките в рудника са т.нар. добивни камери, които са с много големи размери – с височина от 20 -30 метра и дължина, достигаща 100 метра. Задачата на маркшайдерите е да сканират тези минни изработки, да определят техните форма, обем и съответно добитото от тях количество руда, разбира се, по съответните правила. „В „Дънди“ това трябва да става по безопасен начин и дронът осигурява тази безопасност, тъй като не е необходимо маркшайдерите да се доближават дори до обекта, който трябва да бъде сканиран, а могат дистанционно да го направят с помощта на този робот“, обясни Сергей Михалев, главен инженер „Технически служби“.
Дронът е разработен изцяло тук на територията на рудника в Челопеч, като партньорството с Exyn започва преди 5 години. „Те имаха дрон, имаха хардуерни и софтуерни инженери, ние имахме миньори и рудник - така се получи една добра комбинация и с общи усилия изработихме първия автономен дрон, който лети и сканира подземни минни изработки“, разказа Михалев. „Има още една компания в света, която произвежда такова оборудване, но смея да твърдя, че ние и Exyn сме първите“, подчерта той.
Автономността на дрона се изразява в това, че той сам се навигира в празните пространства. При последвалия полет с мисия 30 метра в тунелите на рудника пред нас и обратно, се уверихме - дронът поема изцяло управлението: излита, сканира, връща се и каца.
„Разбира се, за тези 5 години сме счупили не един и два дрона, но този вече си лети нормално и от около 3 години нямаме катастрофи“, похвали се Михалев.
Данните, които събира дронът се виждат на таблета на маркшайдера - облак от точки, който описва максимално коректно минните изработки.
Има една друга система за сканиране на опасни кухини - система Cavity Monitoring System - CMS, при която чрез стик се подава скенерът в празното пространство, а операторът, в случая - маркшайдерът, стои на безопасно разстояние и CMS-системата заснема. Но CMS прави 14 000 точки, а този дрон прави над 10 милиона точки. При него плътността е толкова голяма, че е несъпоставимо, отбеляза главният инженер.
Подземната инфраструктура
Подземната инфраструктура в рудника е между 100 и 120 км., като пътищата са тесни за два автомобила и имат множество байпаси – отбивки за спиране и изчакване за разминаване. Най-дълбоката точка на рудника е 700 метра, но заради надморската височина, реално е повече от 1000 метра. Влиза се по наклонени галерии и постепенно става доста топло. Заради геотермалния градиент, средно на всеки 100 метра, като слизаш на дълбочина, температурата се увеличава с 3 градуса. В рудника естественият градиент е към 25 градуса, като на работните места, от двигателите на машините, е още по-топло, особено при пробивната карета.
По пътя към 700 м. реална дълбочина и обратно, видяхме нееднократно как става разминаването с тежката техника, чрез т.нар. байпаси.
„Има си йерархия в предимството под земята - с най-голямо предимство са машините, които транспортират взривни материали, след това са тежките минни машини – камиони и челни товарачи, след това са спомагателните машини и ние - с джиповете сме с последно предимство“, обясни Симонски. Той сподели, че един началник смяна, за да обиколи всички работни места, минава 60 – 80 км. каране по подземните тунели.
Състоянието на пътищата е много важно, тъй като пряко влияе на производителността на камионите.
На дъното на рудника има трошачен комплекс, където е разположена трошачката и нужното оборудване, за да бъде изкарана рудата на повърхността, има и сонди, много вентилационни врати и станции, които могат да се управляват и дистанционно.
Производството
Рудите от находището в Челопеч са медно-златно пиритни. Основните съдържащи се полезни компоненти в тях са медта, златото и отчасти имат малко сребро.
Тази руда, обаче съдържа и арсен и това е причина да не се преработва на територията на България, тъй като 1990 г. с постановление на Министерски съвет преработката на арсен-съдържащи руди е забранена. „Това е и основната причина ние да търсим пазари извън България, за да може да продаваме нашата продукция – концентратите“, добави Николай Симонски.
Рудата се преработва в обогатителната фабрика, където чрез колективно-селективна флотация се произвеждат два концентрата - медно-златен концентрат, с преобладаващо съдържание на медни минерали и пиритен концентрат, с преобладаващо съдържание на пирит. Основните полезни елементи в двата концентрата са мед, злато и сребро.
Произведените концентрати и отпадък се обезводняват, след което, концентратите се транспортират за продажба, а отпадъкът се транспортира за запълване на свободни камери под земята или депониране в хвостохранилището, посочи Десислава Домусчиева, главен технолог „Обогатяване“.
Специалист от компанията обясни как от кипящата смес става извличането на ценните елементи: „Добавянето на реагент прави неумокряеми минералите, които искаме да извлечем, те се закрепват върху мехурчета и изскачат на повърхността. Това, което правим е да събираме само пяната – тя прелива, събираме я и я обезводняваме. За да получим суровината пречистена, материалът преминава през няколко етапа на флотация. Концентратът прелива от повърхността, а отпадъкът пада на дъното".
Според отчета на компанията, производствените резултати за 2022 г. показват, че са добити 2 130 610 тона руда, преработени 2 138 792 тона руда и са произведени 123 046 тона медно-златен концентрат и 267 642 тона пиритен концентрат.
Къде отива отпадъкът
Отпадъкът от фабриката се транспортира по затворени тръбопроводи в течен вид в хвостохранилището, което е с площ 154 хектара, като е надстроено и има свободен обем над 15 млн. куб. м. за запълване. Съоръжението е така изградено, че водата, която се отделя от отпадъчния продукт да е на разстояние 400 – 500 метра от основната стена и от помощната стена, а водата, която се утаява и се избистря, се връща в производствения процес за използване отново, посочи Георги Божилов, главен инженер „Преработка на руда“. „Част от отпадъчния продукт след флотацията постъпва в сгъстител и след сгъстяване до около 50% твърдо вещество, с поми се транспортира до цех, където се смесва с цимент и с помпи, по тръбопроводи, се изпраща под земята за запълване на камерите, от които е добивана руда“, добави той.
Мониторингът на цялото съоръжение се извършва с автоматизирана система, измерват се и деформациите в основната стена и резултатите се получават в реално време – един път дневно, като има възможност да се промени честотата до 2 минути, съобщи още Божилов.
Той ни показа и завършеното тази година затежняване на основната стена.
600 000 тона материал от местни скали е насипан пред стената за затежняване – за натискане на самата стена, като дренажната вода се хваща и се качва с помпен агрегат и тръбопроводи обратно в утаечното езеро. „От хранилището не излиза нищо навън“, категоричен е главният инженер. Той подчерта, че съоръжението отговаря на най-добрите практики, на канадската асоциация за големите язовири и на глобалния стандарт, който от 2020 г. влезе в сила в ЕС.
В стената е изграден и канал за дъждовни води, изтъкна още Божилов и поясни, че всички води, които идват от източната страна и от северната страна са пресечени с канал, така че дъждовни води не влизат в хвостохранилището, а се извеждат отстрани и посредством канал отиват в дерето.
"В момента прокарваме пиезометри – сондажи, които измерват нивото на водата в тялото на стената и в тези сондажи ще бъдат монтирани сензори, които измерват поровото налягане – налягането на водата, която повдига земния насип и това е част от мониторинговата система за контрол", добави експертът.
Смартцентър и креативност
Целият технологичен процес се планира и управлява от създадения Смартцентър в административната сграда. "От тук се управляват всички видове дейности на целия рудник – пробиване, зареждане, взривяване, извозване и всички помощни сервизни дейности. Взема се информацията в реално време, вижда се къде са отклоненията, има колега, който адаптира плановете, възлага задачите и те стават видими в рудничното назначение", разказа Цветомир Велков, генерален мениджър, „Дънди Прешъс Металс Челопеч“.
Той сподели, че в началото е имало забавяне на данните от кликването в рудника, до виждането им в залата на смартцентъра, но това е преодоляно и вече всичко става в реално време и изцяло оперативното управление на процеси, системи, машини е от тук.
Мониторите предават всичко в реално време - как трошачката под земята работи и натрошената руда влиза във фабриката и следва всички технологични процеси - смилане, флотация, сгъстяване, филтроване, до крайния концентрат, включително и хвостохранилището и бетоновия възел, както и обратното запълнение. Управлението се извършва от тук; взривните дейности се извършват без хора под земята, а от тук; управлението на цялата вентилационна система става дистанционно от тук, подчерта той и ни показа действаща електрическа сонда на дистанционно управление, която може да работи и сама.
Това е добивната сонда, която е без дизелов двигател, а с батерия и работи изцяло на ток. Машината може да работи автономно, може да работи и дистанционно. Тази технология позволява един оператор да управлява 3 машини - имаш оператор под земята за технологичните дейности, които изискват физическа подготовка под земята и имаш един оператор на повърхността, който управлява от 1 до 3 машини, разказа Велков. "Така можеш да използваш периода, който е планиран за проветряване и няма хора под земята, за да генерираш производство от повърхността", подчерта той.
"Всички тези датчици, сензори и камери генерират информация. Ние тръгнахме да правим управление в реално време, защото най-ценното нещо в живота е информацията, но тя е нищо, ако не я използваш така, че да имаш добавена стойност в твоя процес", отбеляза генералният мениджър. Той съобщи, че като следваща стъпка в надграждането на системата, компанията е създала креативен център, където експертите обработват данните и творят и ни заведе при тях.
Моделите за статистически контрол на процесите не са новост - в индустрията "Тойота" първи започват да ги използват, но прилагането им в минната индустрия е новаторско, коментира Николай Киров, директор „Оперативен дизайн“. Той цитира изследване на Маккинзи, според което, в минната индустрия за взимане на решения се използват по-малко от 1% от данните, които се събират и заключи: "Ние се опитваме да сме по-добре".
Още по темата: Уникално съоръжение и най-модерна технология - в най-стария златодобивен рудник в Европа